Learn the Lingo of Towing
Tim Esterdahl | Aug 27, 2014 | Comments 1
Towing a load isn’t a difficult task, however, you shouldn’t just hop in and drive. Here is what you need to know before you tow.
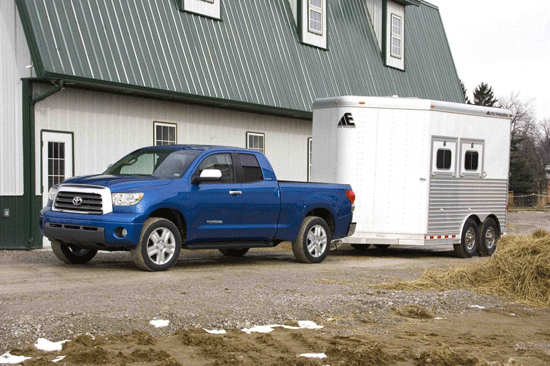
First time towing? Here is a handy guide.
Towing Terminology Basics
Let’s start with some basic terminology.
Ball Mount – The ball mount is the point where the ball is attached to your truck. It can be a short steel tube that’s placed inside the receiver hitch, or it can simply be a hole in the middle of the rear bumper.
Base Curb Weight – This is the weight of a vehicle as defined by the manufacture with standard equipment and a full tank of fuel. It is usually listed on the door jamb and it does not include passengers, cargo or optional equipment.
Bumper Hitch – A bumper hitch is simply the term for a bumper mounting location for a hitch. Bumper hitches are used for lightweight towing.
NOTE: Sometimes a heavy-duty hitch mounted just below the bumper is referred to as a “bumper hitch.” This is incorrect.
Coupler – This mechanism is bolted or welded onto the end of the trailer tongue. The coupler fits securely over and rests/pivots on the trailer ball.
Fifth-Wheel Hitch – This hitch connects the trailer to the bed of the pickup. It resembles the hitch design found on SEMI trucks.
Gooseneck Hitch – A gooseneck hitch is similar to a fifth-wheel hitch in that both connect the trailer to the bed. The main difference is in how they attach. Goosenecks use a ball located in the bed of the pickup with a coupler that is attached to the trailer. A fifth-wheel is the opposite with a coupler in the bed which attaches to a kingpin attached to the trailer.
Gross Trailer Weight (GTW) – An important part of towing is knowing your gross trailer weight. This is simply the weight of the trailer and all the cargo. It is commonly measured by placing the loaded trailer on a vehicle scale. This is often referred to as a trailer’s “wet” weight.
Jack-Knife – This is situation where the truck and trailer are at an extremely sharp angle. It can cause damage to both truck and trailer. This situation commonly occurs when backing up a load.
Pintle Hitch – This is a special hitch which is commonly used in the military, agricultural and construction industries when towing large equipment.
Safety Chain(s) – This chain is required by law and should be crossed under the tongue of the trailer. The idea is that if the tongue happens to drop from the hitch, it will not make contact with the road surface. Most truck owners will use two safety chains, some heavy trailer owners will use more.
Sway Control – This is typically an electronic feature that helps control unwanted lateral movements by the trailer. However, there are some mechanical sway control devices that sit between the trailer and the tow vehicle, and combat sway using a friction pad and an expandable connection.
Tongue Weight (TW) – Another vital piece of information is the trailer tongue weight, or the portion of the trailer’s weight that the two vehicle must carry. The tongue weight will change based on where the load sits on the trailer, and a rouge estimate is to assume 10-25% of a trailer’s weight will rest on the tongue. This, in turn, will dictate the size of truck used to pull the trailer, as a truck shouldn’t pull a trailer with a tongue weight that’s higher than the payload rating.
Trailers with multiple axles tend to have lower tongue weights (as a percentage of total weight) than trailers with single or dual axles.
Trailer Ball – This is the object that connects the trailer hitch to the trailer.
Weight Distribution Capacity (WD) – This is the measure of total weight a trailer can pull with a weight distribution system installed.
Trailer Hitch Classes
There are a variety of trailer hitches on the market and it is important to get the right one for the job.
Class I Receivers
- Towing capacity up to 2,000 pounds GTW and 200 pounds TW
- 1¼-inch receiver hitch opening
- Uses a ½-inch pin to secure the ball mount in place
- Will work with hitch balls with ¾-inch-diameter shank
Class II Receivers
- Designed for light towing
- Towing capacity up to 3,500 pounds GTW and 350 pounds TW
- 1¼-inch receiver hitch opening
- Uses a ½-inch pin to secure the ball mount in place
- Will work with hitch balls with ¾-inch-diameter shank
Class III Receivers
- Designed for trucks, vans and SUVs
- Towing capacity up to 6,000 pounds GTW and 600 pounds TW
- Works with all Class III accessories
- Can work with Class I and Class II hitch accessories with an adapter
- 2-inch receiver hitch opening
- Will work with hitch balls with 1-inch-diameter shank
Class IV Receivers
- Designed for trucks, vans and SUVs
- Towing capacity up to 12,000 pounds GTW and 1,000 pounds TW
- 2-inch receiver hitch opening
- Works with all Class III and IV accessories
- Can work with Class I and II hitch accessories with an adapter
- Uses a 5⁄8-inch pin to secure ball mount in place
- Class IV hitch balls require a 1¼-inch-diameter shank
Class V Receivers
- Designed for heavy-duty trucks or vans to tow large trailers
- Towing capacity up to 18,000 pounds GTW and 1,800 pounds TW
- 2½-inch receiver hitch opening
- Can use Class III or IV accessory with a reducer sleeve
- Class V hitch balls require a 1¼-inch-diameter shank
Picking the Best Ball Mount
When it comes to hooking up your load, the first step is to make sure you have the best ball mount for the job. The idea is to have a ball mount that fits the coupler and creates a level ride. Towing a load with a ball that is either too high or low will put additional strain on the connection and may result in damaging the truck/trailer and/or creating a difficult ride.
The first step to finding the correct ball is to measure the distance from the ground to the coupler and the hitch. Make sure you do this on a level surface. With this information, you can determine what type of hitch adaptation you may need. For example, if the hitch is higher, you will need to use a drop mount. If the coupler is higher, you will need a mount with a rise.
Electronic Brake Controllers
Another key item when towing is a brake controller. This device helps ensure that the trailer brakes activate slightly before the truck’s braking system. That way, the truck will never decelerate faster than the trailer…preventing situations where the trailer swings around sideways.
In order to use an electronic brake controller, you’ll want some brake controller wiring (most newer trucks include wiring from the factory), and of course your trailer must have functional brakes.
Finally, once you’ve got everything connected, you’ll want to configure the “grabbiness” of the trailer’s brake system in response to your truck’s brake system. Again, the idea is to make sure the trailer brakes harder/earlier than the truck (at least under heavy braking).
NOTE: Many new trucks include a built-in trailer brake controller, which is vastly superior to most after-market trailer brake controllers.
Types of Electronic Braking Controllers
There are primarily two types of brake controllers on the market: proportional and time delayed.
Proportional – This system determines how much braking the tow vehicle is using and it proportionally uses the same amount for the trailer. This controller provides the smoothest and quickest brakes with the least amount of wear and tear. However, it is also the more complex system.
Time-Delay – This system is arguably the more user-friendly option and least complex. This system uses a user-set device in the cab to determine how much braking power the trailer should apply. Basically, when you engage the brakes in the cabin, the system sends a predetermined amount of power to the trailer. The user can then set the amount of braking to their preference. Using this device usually results in uneven brake wear since both systems are engaged at different stopping rates.
Additional Safety Systems – Weight Distribution, Sway Control
There are two other common safety systems that need mentioned.
Weight Distribution – One of the crucial items to consider when towing is how the weight is distributed throughout the load. If your load has the majority of weight on any part of your trailer, your load may stop harshly or sway. This is why a weight distribution system makes sense. This system helps transfer the load applied to the rear of the tow vehicle and the tongue weight to all the axles on both the tow vehicle and trailer. This creates a smoother ride and helps you increase the maximum capacity of your hitch.
Sway Control – A common problem when towing is a trailer swaying laterally while driving. This often occurs when driving through crosswinds, a load not properly distributed or windy roads. The fix is to introduce an independent, friction-style sway control. This device bolts onto the trailer frame at one end and attaches to the hitch with a secondary ball at the other. It works by telescoping an interior bar back and forth as the trailer sways.
There are also a dependent and active sway control bars which are commonly found as part of a weight-distributing system. They both work about the same as a friction-style by counteracting the loads sway.
When it comes to towing, the more you know, the better you will tow. Reference this guide before you tow to create a safe and enjoyable experience.
Filed Under: Tundra Towing
The IBCs:
The entire trailer braking industry has been changing their technologies for over 60 years now. Way too many types and methods to discuss here.
About 15 years ago some major advances were made in Australia to finally develop workable and reliable electric over hydraulic trailer braking systems.
Ultimately the goal was to provide better, smoother, and more reliable trailer braking systems that could begin to match the tow vehicle’s braking performance and responsiveness. Surge brakes and traditional electric brakes are unable to match that type of performance.
There is great clamor for IBC’s in today’s trucks, even by 80% of the owners that never tow. Of course much of this has come from Ford’s insanely successful marketing machine. Ford’s own IBCs have only been limited to electric brakes only (completely useless for boat owners) for almost the entire time Ford has been providing IBCs. It has only been during the last four years that Ford has begun releasing IBCs in their trucks for a “limited” number of electric over hydraulic systems; and even then not all of the features of the more advance braking systems are accommodated by the IBCs.
Whether or not Toyota can offer an IBC’s that can provide all the benefits of the more advanced electric over hydraulic along with fully seamless integrated ABS remains to be seen? Time will tell I guess.