CGI Engine Blocks and Half-Ton Diesels – What, How, and Why
Benjamin | Feb 23, 2011 | Comments 2
Sometimes some of the most innovative design ideas rely on concepts that are actually very, very old. History is littered with theories, materials and feats of engineering that were patented long before their time, intriguing developments that simply were not capitalized on in their era for a variety of different reasons. One technology that falls under this general heading is compacted graphite iron.
Compacted graphite iron (CGI) was developed more than 60 years ago as a high strength alternative to standard gray iron. In fact, CGI is 75 percent stronger and stiffer than traditional gray iron, and it also offers better resistance to fatigue than both aluminum and gray iron. This strong and lightweight material was used only sparingly over the decades following its discovery, with applications including high speed train brakes and commercial diesel truck engines.
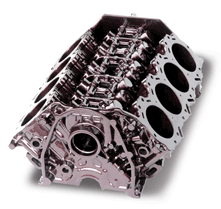
CGI Engine Block
In a more modern setting, CGI has found its way into the factories that produce premium luxury cars, such as those run by BMW and Audi who use the metal in a number of different engine designs. Jaguar and Hyundai have also adopted the use of CGI in several high performance applications. In the motorsports world, NASCAR has heavily adopted CGI technology, with the majority of teams using this material for their engine blocks which see some of the harshest abuse that a motor can take. Even TRD has gotten into the act, using a CGI block for its Craftsman series racing truck engine.
For half-ton truck owners, the most intriguing possibilities offered by compacted graphite iron relate to its potential in the lightweight diesel field. Traditionally, diesel V-8 engines have been restricted to three-quarter or full ton truck platforms, due in part to the heaviness of these drivetrains. In fact, some diesel motors can weigh as much as six times more than their gasoline equivalents due to the strength needed in the engine block. CGI offers not only significantly reduced engine weights – in some cases as much as 20 percent – but also more power from similar displacements due to the design advantages offered by the material.
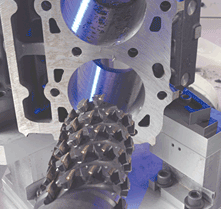
CGI Engine Block Being Machined
As of now, compacted graphite iron has not found its way into the U.S. pickup truck scene, which is where it could potentially make its greatest impact in the half-ton segment of the market. The fuel economy benefits offered by diesel engines have typically been offset by the heavier designs of 2500 and 3500 series trucks, but if a lightweight diesel motor can be shoehorned into a 1500 series pickup, then the torque and miles per gallon provided by diesel would finally find their full expression. New machining techniques and a greater acceptance of CGI engine designs are bringing this particular technology that much closer to production reality in the light truck world.
Hopefully, this technology will make it possible for Toyota to build a diesel Tundra (fingers crossed).
Filed Under: Diesel Tundra
You must be totally uninformed
http://www.sintercast.com/
Alf – It would be more appropriate to comment if you could elaborate on what, specifically, we missed. I’m not a materials expert, but I understand the basics and from what I can tell the article honors the information on the site you referenced.
Can you expand on why we’re uninformed, or is this just good old fashioned trolling?